CONSTRUCTION
Step-by-Step Guide to Rock Revetment Construction
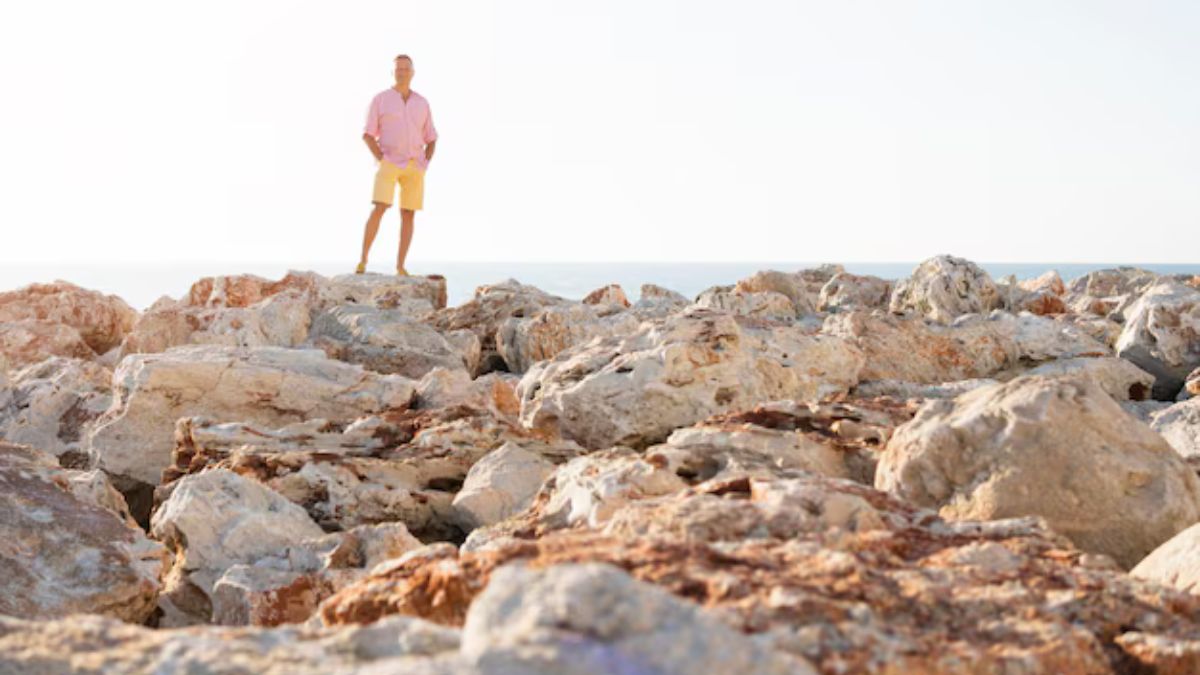
Rock revetment construction is an effective method for protecting shorelines, riverbanks, and coastal areas from erosion and wave action. The use of natural materials, such as rocks and boulders, creates a robust barrier that can withstand the forces of nature. In this article, we will delve into the step-by-step process of constructing a rock revetment, exploring the materials, design considerations, and construction techniques involved. Whether you are a civil engineer, landscape architect, or a property owner looking to safeguard your land, this guide will provide valuable insights into the construction of rock revetments.
Understanding Rock Revetments
Before diving into the construction process, it is essential to understand what rock revetments are and their purpose. A revetment is a structure built to absorb and deflect the energy of waves and currents, ultimately preventing erosion. Rock revetments are often preferred due to their natural appearance and ability to blend into the surrounding environment. They can be used in various applications, including coastal protection, riverbank stabilization, and flood control. According to the U.S. Army Corps of Engineers, properly designed and constructed rock revetments can significantly reduce erosion rates, making them a popular choice in many engineering projects.
Initial Planning and Site Assessment
The first step in constructing a rock revetment is thorough planning and site assessment. This phase involves analyzing the site’s specific conditions, such as soil type, wave action, and erosion patterns. Conducting a topographic survey and hydrological analysis is crucial to understanding how water interacts with the landscape. Additionally, it is essential to check local regulations and permits required for construction. Engaging with civil engineers and environmental specialists can provide valuable insights into the best practices for your specific site. Remember that a well-planned revetment can save costs and ensure long-term effectiveness.
Design Considerations
Once you have assessed the site and gathered relevant data, the next step is to design the rock revetment. The design should consider the size and type of rocks to be used, as well as the slope of the revetment. The angle of the slope is crucial for stability; a typical slope ranges from 1:1 to 2:1 (horizontal to vertical). Additionally, the design should account for drainage to prevent water from pooling behind the revetment, which can lead to failure. Various design software tools are available to aid in creating effective designs, and consulting with experienced engineers can ensure that the design meets structural and environmental standards.
Material Selection
The choice of materials is a critical aspect of rock revetment construction. The rocks used must be durable and resistant to weathering and erosion. Common materials include granite, limestone, and basalt, as these rocks possess the necessary strength and longevity. The size of the rocks is also important; larger rocks provide better resistance against wave action, while smaller rocks can fill gaps and provide stability. It is advisable to source materials locally when possible to minimize transportation costs and environmental impact. Additionally, incorporating biodegradable materials such as coir mats or geotextiles can enhance stability and promote vegetation growth.
Preparation of the Construction Site
Before construction begins, the site must be adequately prepared. This involves clearing the area of any vegetation, debris, or existing structures that may interfere with the revetment. Excavation may be required to create a stable foundation for the rocks. The foundation should be level and compacted to support the weight of the revetment. Additionally, it is essential to create a drainage system to redirect water away from the foundation, reducing the risk of erosion and ensuring the longevity of the revetment. Proper site preparation lays the groundwork for a successful rock revetment construction project.
Construction Process
The actual construction of the rock revetment involves several steps. Start by placing the larger rocks at the base of the revetment, ensuring they are tightly packed and interlocked to create a stable foundation. This base layer is critical for resisting wave forces and preventing erosion. Following the placement of the larger rocks, gradually add smaller rocks and fill materials to create a slope that follows the designed angle. Ensure that each layer is compacted and leveled to prevent shifting over time. Regularly check for evenness and stability as you progress through the construction process.
Quality Control Measures
Implementing quality control measures throughout the construction process is essential to ensure the effectiveness of the rock revetment. Regular inspections should be conducted to identify any issues with rock placement, settling, or erosion. It is crucial to address any problems immediately to prevent long-term damage. In addition, testing the drainage systems during and after construction can help ensure that water flows correctly and does not compromise the revetment’s stability. Documenting the construction process, including photographs and measurements, can also serve as a valuable resource for future maintenance and assessments.
Post-Construction Maintenance
After the construction of the rock revetment is complete, ongoing maintenance is vital for its longevity and effectiveness. Regular inspections should be scheduled to monitor for signs of erosion, displacement, or structural failure. It is essential to address any issues promptly to maintain the integrity of the revetment. Additionally, promoting vegetation growth can help stabilize the area and reduce erosion in the surrounding landscape. Establishing a maintenance plan that includes periodic assessments and necessary repairs will ensure that the rock revetment continues to provide effective protection for many years to come.
Conclusion
including thorough planning, careful material selection, and ongoing maintenance, you can ensure the effectiveness and longevity of your revetment. Understanding the various aspects of rock revetment construction, from site assessment to post-construction care, will enable you to make informed decisions and successfully safeguard your property against the forces of nature. In a world increasingly affected by climate change and rising sea levels, the importance of effective erosion control cannot be overstated.
CONSTRUCTION
Maximize Roof Lifespan: Homeowner Maintenance Tips
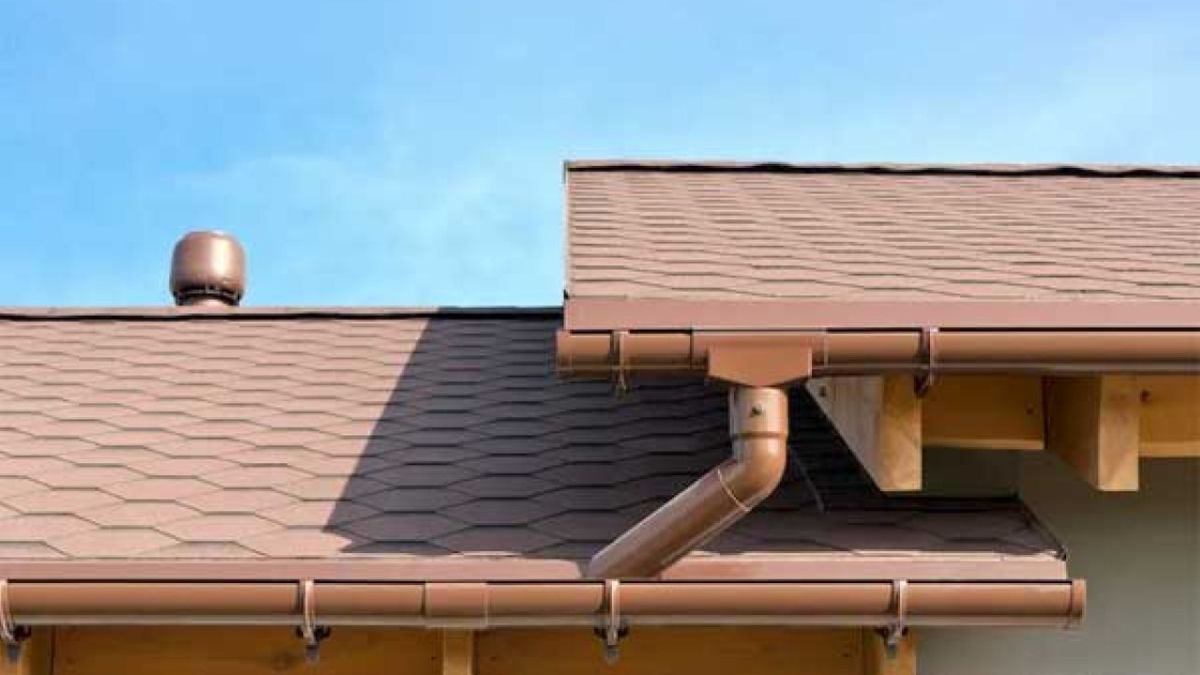
The Importance of Roof Maintenance
Roof maintenance is essential to house care, which may significantly increase your home’s lifespan and protect it from environmental threats. A roof does more than cover the top of your house; it acts as the primary defense against rain, snow, wind, and sun. Maintaining this essential barrier is crucial for preserving the safety and value of your home. Homeowners can save money on repairs, protect their family’s health, and increase energy efficiency by taking a proactive approach to maintenance. Regardless of the weather, this all-encompassing strategy helps guarantee that your house stays a sanctuary. For those looking to enhance their roof care routine, consulting with the best roofers in Tulsa can provide tailored solutions and expert insight.
Regular Roof Inspections
Regularly conducting inspections is the most critical maintenance task homeowners can undertake. These inspections should be scheduled at least twice a year, preferably during spring and fall, to capture potential damage caused by seasonal weather changes. During an inspection, assess the condition of shingles, flashing, and any roof penetrations, such as chimneys and skylights. It’s also critical to clear away debris like leaves and branches and look for mold growth or water damage indications. Keeping an eye out for sagging areas or loose materials can help you take timely action before minor faults develop into extensive and expensive repairs. By staying vigilant, you can maintain a watertight environment and extend the roof’s life by several years, preserving its function and visual appeal.
Cleaning Gutters: A Simple Yet Crucial Task
Gutters may seem like a secondary aspect of your roofing system, but they are indispensable in protecting your home from water damage. To minimize erosion, leaks, and potential basement flooding, gutters aim to divert rainfall away from your home’s foundation and structural elements. This helps to prevent floods in the base of your home. Regular cleanup involves removing accumulated organic material, such as dirt, twigs, and leaves, to avoid overflowing. Ment. Regular cleanup involves removing accumulated organic material, such as dirt, twigs, and leaves, to prevent overflowing. These blockages can cause water to seep into the roof’s edge, resulting in wood rot and architectural damage. Addressing this keeps your roof and home foundation dry and secure and helps preserve your home’s landscaping by directing water to desired areas.
Identifying and Dealing with Roof Damage
Storms, strong winds, and hail are weather phenomena that can seriously harm roofs. Identifying and rectifying these damages promptly is vital for maintaining roof integrity. After severe weather, inspecting the entire surface for missing shingles, exposed or rusting nails, blistering paint, and other visible signs of damage is crucial. The Family Handyman asserts that quick fixes are necessary to avoid leaks, potentially expensive structural damage, and aesthetic concerns. Utilizing materials that match the existing roof color and texture ensures a seamless repair, helping maintain your home’s aesthetic while securing its defenses against future weather events.
Preparing Your Roof for Harsh Weather
The effects of extreme weather can’t be underestimated, and preparing your roof can mitigate many potential problems. This preparation involves routine checks and strengthening the roof elements to endure adverse conditions such as high winds, ice, and snow. This can include installing additional supports or sealing vulnerable areas with weather-resistant materials. Ensure to remove overhanging tree limbs that could snap and damage the roof during a storm. By preparing your roof for inclement weather, you reduce the likelihood of damage and can rest easier knowing your home is well-protected from the elements.
The Role of Proper Insulation
Insulation plays an unsung hero in the longevity and efficiency of roofing systems. A more stable indoor climate and cheaper energy costs are two benefits of maintaining proper insulation, which reduces heat gain or loss. During winter, adequate insulation keeps warmth inside, reducing the need for constant heating. Conversely, it helps keep your home cooler during sweltering summers. Effective insulation supports family comfort and reduces the wear on roofing materials. Over time, limited exposure to extreme temperatures and moisture-related issues can preserve the roof’s structural elements, adding longevity and reducing maintenance costs.
When to Call in the Professionals
While homeowners can handle many roofing maintenance tasks homeowners can handle, there comes a point when professional assistance is necessary. Your ability to recognize complex issues that require expert assistance is essential to preserving the longevity and health of your roof. Structural damage or extensive leaks may necessitate specialized skills and equipment for proper repair. As noted in professional guides like those from This Old House, professionals can provide safety and quality assurance that DIY repairs often cannot. Engaging with industry experts ensures that issues are identified and resolved effectively, preserving the structural integrity of your roof over the long term.
Sustainability and Roof Longevity
Incorporating sustainability into roofing can benefit the environment and your home’s longevity. Sustainable roofing solutions, such as energy-efficient materials or solar panel installations, reduce the homeowner’s carbon footprint and often increase the roofing system’s durability and lifespan. As options like cool roofs or green roofs gain popularity, they offer cost-saving benefits alongside environmental ones, ensuring your roof continues to protect and serve efficiently over the decades. This holistic approach to roofing contributes to a resilient future for homeowners and communities.
CONSTRUCTION
Maximising Efficiency with Wet Hire Excavator Solutions
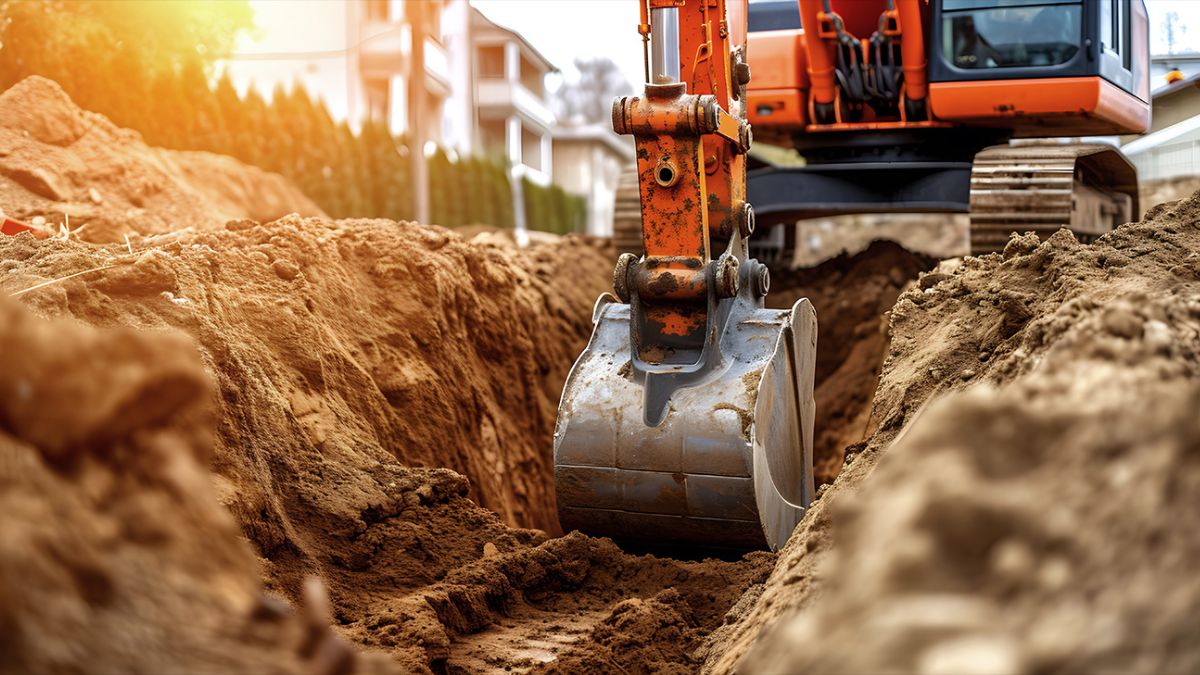
In the realm of construction and excavation services, efficiency is not just a goal but a prerequisite for success. One of the key components to achieving this efficiency is choosing the right approach to equipment hire, and specifically the benefits of choosing a wet hire excavator solution. This article is set to explore the fundamental advantages of opting for wet hire options, and how construction projects can harness this approach to streamline operations, reduce downtime, and ultimately improve their bottom line.
The Concept of Wet Hire in Excavation Services
For those unfamiliar with the term, ‘wet hire’ refers to the practice of hiring equipment that comes with its own operator. This is contrary to ‘dry hire,’ which is the rental of equipment alone, without any additional manpower provided. With the complex nature of excavators and their pivotal role in various construction projects, wet hire presents itself as a compelling choice for many contractors.
Expertise and Experience on Demand
When you choose a wet hire excavator, you are not just paying for the machine but also the expertise of an experienced operator. This immediately elevates the level of precision within a project. Experienced operators bring with them extensive knowledge about the intricacies of the machinery, ensuring that all excavations are performed with the highest degree of professionalism and adherence to safety protocols.
Reduced Training and Recruitment Hassles
One of the challenges in the construction industry is finding and training skilled equipment operators. By selecting a wet hire solution, companies are relieved of the burden of recruitment and training. The provider of the wet hire service is responsible for ensuring that their operators keep abreast with the latest industry standards and competencies. This means that construction projects can commence more swiftly, sidestepping the time-consuming steps involved in bringing new hires up to speed.
Minimising Downtime and Maximising Productivity
Every construction project has strict deadlines, and any unplanned downtime can result in financial loss and project delays. The assurance of having a proficient operator can significantly minimise machine downtime. Wet hire operators can identify and resolve minor mechanical issues on site, reducing the need for frequent maintenance stops. Their adept handling of the equipment optimises the machinery’s run-time further maximising productivity on-site.
Adapting to Project Complexity with Ease
Excavation work can vary greatly in complexity, from the nuances of urban construction to the challenges presented by large-scale rural developments. Wet hire excavators come with operators who are often versed in a wide range of conditions and project types, offering versatility to construction firms. This adaptability is particularly valuable when dealing with unexpected ground conditions or navigating complex job sites without a hitch.
Cost-effectiveness of Wet Hire Solutions
While the initial outlay for a wet hire service can seem higher than dry hire, the long-term cost-effectiveness of this option can be significant. By reducing the likelihood of incorrect operation leading to equipment damage or inefficiency, wet hire solutions can ward off additional repair costs. Furthermore, as the hire includes operator fees, companies save on the overhead costs associated with employing an in-house operator, like salaries and benefits.
Risks Mitigation with Wet Hire Excavators
The excavation process carries inherent risks, from damaging underground utilities to potential cave-ins. Wet hire solutions inherently reduce the level of risk by providing operators who can navigate these hazards expertly. Their focused adherence to safety procedures ensures operational compliance and mitigates against the potential for accidents and the associated liabilities.
Compliance with Environmental and Legal Standards
Construction and excavation practices are bound by stringent environmental and legal standards. Wet hire operators are usually well-versed in these requirements and can ensure that work is conducted in a manner that upholds relevant regulations, helping project managers to navigate the maze of compliance without fretting over potential violations.
Streamlining Project Management
With the presence of a dedicated operator, project managers can better focus their attention on overseeing the broader aspects of the construction initiative. Knowing that the wet hire provider manages part of their workforce streamlines various management duties, potentially saving time and allowing for more efficient allocation of human resources.
Choosing the Right Wet Hire Excavator Provider
While the benefits of wet hire solutions are clear, the quality of the service largely depends on the provider. Businesses should seek out wet hire providers with a robust reputation, a fleet of well-maintained and modern excavators, and a transparent approach to customer service.
Conclusion
Wet hire excavator services bring professionalism, efficiency, and peace of mind to construction projects. They signify a comprehensive solution that couples state-of-the-art machinery with skilled operators, culminating in a potent formula for seamless excavation operations. In an industry where every aspect of timing, precision, and compliance is critical, wet hire solutions stand out as a strategic choice for contractors aiming to maximise efficiency and project outcomes.
In summary, the decision to opt for a wet hire excavator is a proactive step towards ensuring the highest degree of efficiency. Thanks to the combination of skilled labour, reduced downtime, and expert management of the equipment, wet hire offers a competitive edge that can substantially influence the success of any excavation project.
CONSTRUCTION
The Future of Construction: Embracing Digital Transformation
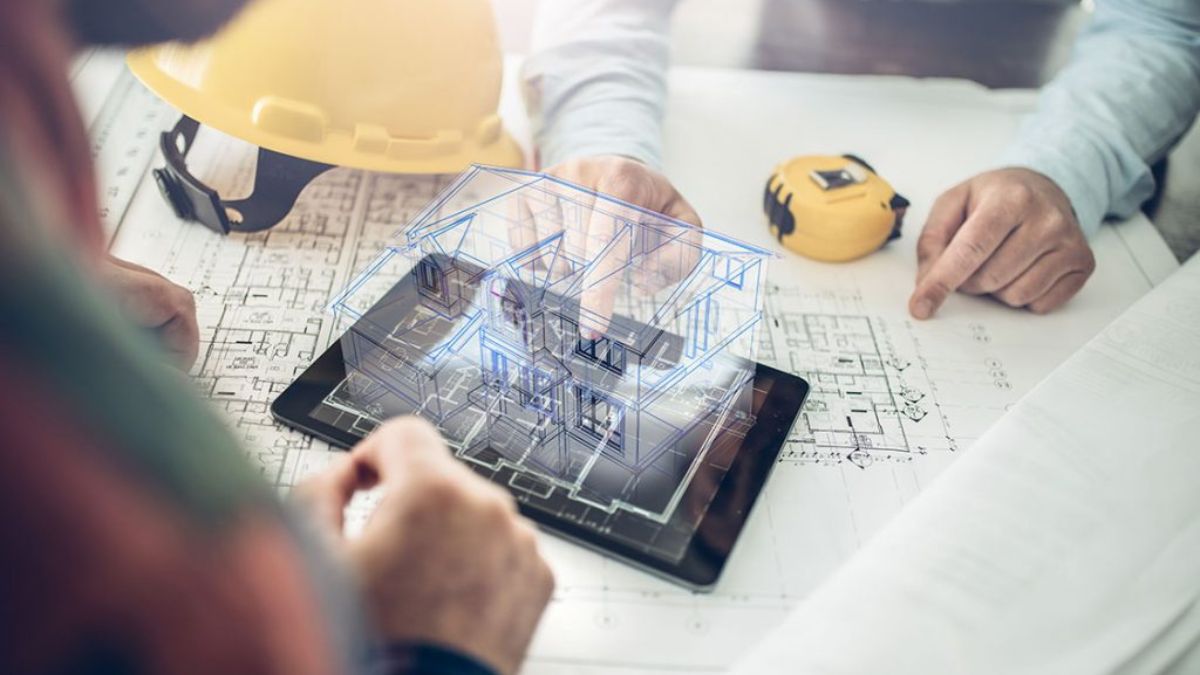
The Role of Digital Transformation in Modern Construction
Traditionally known for its reliance on manual labor and conventional processes, the construction industry is experiencing a profound shift. Digital transformation has emerged as a game-changing force, introducing a new era of efficiency and innovation. This transformation extends beyond integrating new gadgets and software; it fundamentally alters how projects are conceptualized, managed, and delivered. By streamlining communication and automating routine tasks, these digital solutions empower teams to focus on more complex challenges, thus increasing overall productivity. According to a McKinsey report, industries that embrace digital technologies witness considerable advancements in speed, accuracy, and cost-effectiveness.
Key Technologies Driving Digital Change
- Artificial Intelligence (AI): Integrating AI in construction creates a paradigm shift. With AI-driven predictive analytics, construction firms can foresee potential issues before they become critical, optimizing resource allocation and improving decision-making processes. By analyzing data patterns, AI tools can suggest the most efficient pathways for project development, streamlining operations significantly. Amidst this transition, tools like the virtual construction assistant are quickly becoming indispensable.
- Building Information Modeling (BIM): BIM is a digital representation of a building’s characteristics, offering a multi-dimensional insight into the project’s lifecycle. This capability enhances visualization and fosters collaboration among architects, engineers, and contractors. BIM’s robust data-sharing capabilities ensure that all stakeholders are on the same page, reducing misunderstandings and ensuring smoother project execution.
- Robotics and Drones: As construction sites embrace automation, robotics and drones are rising. Drones assist in aerial inspections, capturing data from previously hard-to-reach angles and presenting real-time information that improves site safety and operational efficiency. Similarly, robotics are increasingly leveraged to handle tasks that require precision, thereby minimizing human error and enhancing safety standards.
Benefits of Digitizing Construction Processes
Digitizing construction processes brings about several advantages that directly impact project outcomes. Traditional construction methods often suffer from bottlenecks, causing delays and cost overruns. By embracing digital tools, these inefficiencies can be drastically reduced. For instance, adopting BIM allows for virtual simulations before actual construction begins, which can prevent costly errors. Additionally, using software to track project milestones in real-time ensures that any delays are immediately identified and can be addressed promptly. According to industry insights, companies that invest in technology have seen up to a 30% increase in project efficiency, enhancing both the speed and quality of delivery.
Collaboration and Skills Development: The Human Element
While technology is at the heart of digital transformation, the human element remains equally important. Effective collaboration necessitates an environment where team members are empowered to adapt to new tools, which requires ongoing education and skills development. Companies must invest in training programs that help employees effectively understand and use new technologies. This investment yields a workforce that is not only technologically adept but also agile and responsive to change. By fostering a culture of continuous learning, organizations can ensure that their teams remain at the forefront of innovation, ready to capitalize on the benefits of digital tools.
Challenges and Considerations in Digital Adoption
Despite the clear advantages, the road to successful digital adoption has challenges. Initial costs associated with purchasing and implementing new technologies can be substantial. Companies must also tackle the learning curve that comes with new systems, which can lead to temporary productivity dips. Resistance to change is another hurdle, often fueled by a lack of understanding or fear of the unknown. To overcome these challenges, construction firms need strategic planning that clearly outlines digital transformation’s benefits and a supportive transition framework. Encouraging open dialogue and providing adequate support can mitigate these risks and facilitate a smoother transition to a digital-first approach.
Case Studies: Successful Digital Transformations
Numerous construction companies have restructured their operations around digital solutions, with impressive results that speak volumes about the potential of technology in this sector. For instance, by integrating comprehensive BIM solutions, some projects have reported faster completion times and significant compliance and quality standards improvements. These real-world examples underline the transformative power of digital tools, proving that when implemented effectively, technology can lead to important advances in efficiency, accuracy, and profitability for construction projects across the globe.
The Future Landscape: What to Expect
As digital transformation continues to evolve, the construction industry’s landscape will see even more innovative technologies emerge. The future promises deeper AI integrations, allowing more intuitive project management tools to anticipate needs and suggest improvements. Wearables may become standard equipment on job sites, monitoring health metrics and ensuring safety regulations are met in real time. Staying ahead of these trends will provide a substantial competitive advantage, underscoring the importance of maintaining a proactive approach to technology adoption in the ever-evolving construction sector.
-
TOPIC5 months ago
7 Expert Tips For Choosing The Best Basement Renovation Companies
-
BUSINESS1 day ago
Top 5 Features of Sowix Online That Every User Should Know About
-
TOPIC4 days ago
Greece Katz Martian: A Cultural Exploration of an Intriguing Figure
-
TOPIC1 month ago
Top Features of BetterThisWorld .com You Need to Know About
-
FINANCE2 months ago
How TraceLoans Can Simplify Your Finances
-
TOPIC7 days ago
Kashito_Toto Explained: What You Should Know in 2024
-
TOPIC2 months ago
Exploring Sifangds: The Hidden Gem of Modern Design
-
TECHNOLOGY14 hours ago
What is 127.0.0.1:62893? Exploring Localhost Port Numbers