TOPIC
DIY Hijabhoojup: Step-by-Step Guide to Mastering the Look
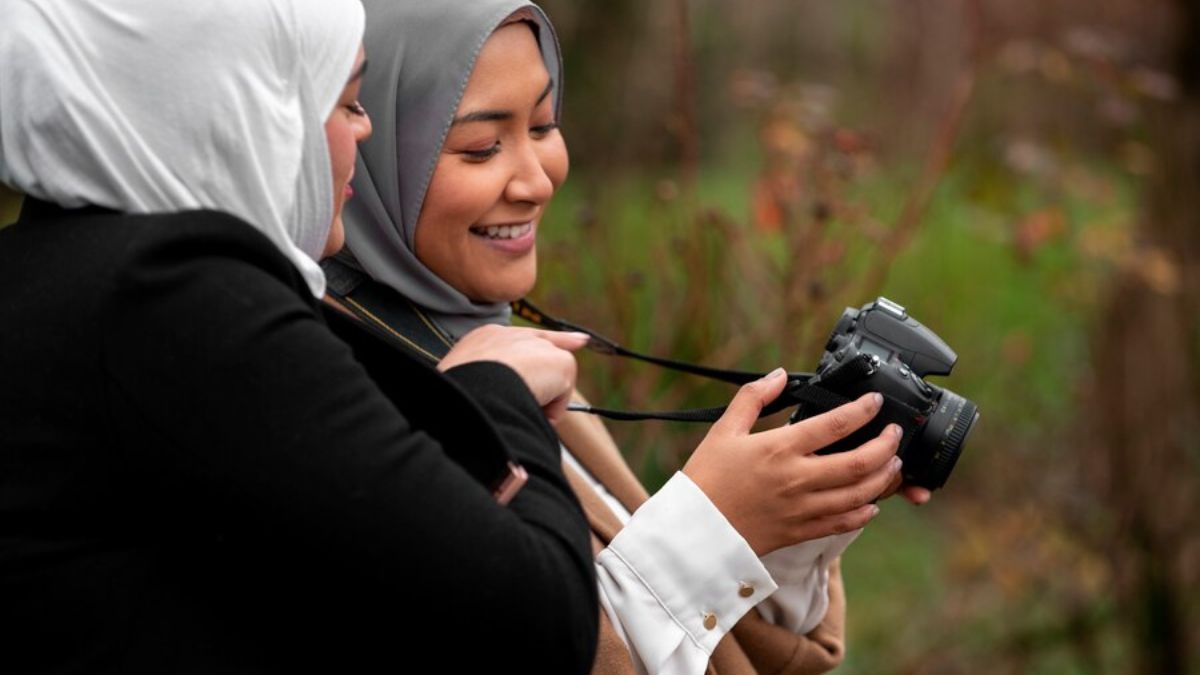
Are you ready to elevate your style and embrace the art of hijabhoojup? This trendy head wrap is not just a fashion statement; it’s a beautiful expression of culture and creativity. Whether you’re looking for an everyday look or something special for an event, mastering the hijabhoojup can add flair to any outfit. Dive into this fun DIY journey where you’ll learn how to create your perfect hijabhoojup from scratch. Let’s explore the benefits, tools needed, and step-by-step instructions that will have you rocking this stunning look in no time!
Benefits of DIY Hijabhoojup
Creating your own hijabhoojup offers a unique blend of style and personal expression. By designing it yourself, you can tailor the look to match your personality and preferences.
DIY projects often lead to savings too. Instead of purchasing expensive ready-made options, crafting at home allows you to use materials that fit your budget.
Additionally, making a hijabhoojup grants you control over the fabric choices. You can select breathable materials for comfort or vibrant colors for those special occasions.
Moreover, this process fosters creativity. Each stitch is an opportunity to explore patterns and styles while honing your sewing skills.
DIYing promotes sustainability by reducing waste associated with mass-produced fashion items. Embracing this trend supports ethical fashion habits while showcasing individuality in every piece created.
Tools and Materials Needed
To create your own hijabhoojup, gathering the right tools and materials is essential. Start with fabric that suits your style and comfort. Cotton or chiffon works well for breathability.
Next, you’ll need measuring tape to ensure precise cuts. A pair of sharp scissors will help create clean edges. If you’re opting for sewing, a sewing machine can save time; otherwise, fabric glue is perfect for no-sew versions.
Don’t forget about pins to hold everything in place while you work. Embellishments like beads or sequins can add flair—get creative!
Have an iron handy; it helps smooth out wrinkles and gives a polished finish to your hijabhoojup. With these essentials on hand, you’re all set to begin crafting your unique look.
Step 1: Choosing the Right Fabric
Choosing the right fabric for your hijabhoojup is crucial. It sets the foundation for both comfort and style.
Consider breathable materials like cotton or chiffon, especially if you’ll wear it for long periods. These fabrics provide airflow while draping elegantly.
Next, think about the climate in which you’ll be wearing your hijabhoojup. Lightweight options are perfect for warmer weather, while heavier fabrics like jersey can offer warmth during cooler months.
Don’t forget to explore different textures and patterns! A soft silk blend can add a touch of luxury, while vibrant prints can make a bold statement.
Consider how easy the fabric is to manage. If you’re new to DIY projects, go for something that’s forgiving and easy to work with as you perfect your technique.
Step 2: Measuring and Cutting the Fabric
Measuring and cutting your fabric is a crucial step in creating a perfect hijabhoojup. Start by laying out your chosen material on a flat surface. This ensures you have enough space to work with.
Using a measuring tape, determine the length and width based on your desired style. Typically, aim for around 2 yards for optimal coverage and drape. Mark these measurements clearly with tailor’s chalk or fabric markers.
Once marked, it’s time to cut carefully along the lines. A sharp pair of scissors makes this task easier and cleaner. Take your time during this process; precision here sets the foundation for your final look.
Remember to leave some extra fabric at the edges if you plan on hemming later. This little detail can enhance durability while keeping fraying at bay as well!
Step 3: Sewing or No-Sew Options
When it comes to creating your hijabhoojup, you have two main options: sewing or no-sew methods. Each has its charm and practicality.
If you’re comfortable with a needle and thread, sewing provides durability. You can create clean hems and secure seams that will last for years. Choose a straight stitch for simple edges or experiment with decorative stitches for added flair.
On the flip side, if you’re not quite ready to tackle a sewing machine, no-sew techniques are equally effective. Fabric glue is an excellent alternative for quick fixes. Simply apply it along the edges to prevent fraying while maintaining flexibility.
You can also opt for fabric tape or even safety pins as temporary solutions. These methods allow you to easily change styles without commitment, making them perfect for beginners exploring their creativity in hijabhoojup design.
Step 4: Adding Embellishments
Adding embellishments to your hijabhoojup can elevate the entire look. Think about what reflects your personal style.
Beads, sequins, or lace trims are popular choices. They can add a touch of glamour without being overwhelming. Carefully sew or glue these elements onto the fabric for a unique flair.
Consider using embroidery as well. It’s an artful way to incorporate intricate designs and patterns that tell a story. Start small if you’re new to it; simple floral motifs work wonders.
Ribbons and brooches also provide versatility in styling. You can tie a ribbon around the hijabhoojup for a chic finish or pin on a decorative brooch for some sparkle.
Remember to balance embellishments with your outfit’s overall theme. The goal is enhancement, not distraction, so choose wisely!
Styling Tips for Different Occasions
For casual outings, opt for lightweight fabrics in pastel shades. A simple draping style paired with a denim jacket can create a relaxed yet chic look.
When attending formal events, consider richer colors like deep burgundy or navy. Layer your hijabhoojup gracefully and accessorize with statement earrings to elevate the ensemble.
For work settings, choose neutral tones that blend well with professional attire. A sleek wrap technique maintains an elegant silhouette while ensuring comfort throughout the day.
During festive occasions, don’t shy away from vibrant patterns and textures. Incorporate sequins or lace details into your hijabhoojup to reflect the joyous spirit of celebration.
Outdoor activities call for breathable materials. Style your hijabhoojup in a way that allows movement while keeping you effortlessly stylish under the sun.
Maintenance and Care for Your Hijabhoojup
To keep your hijabhoojup looking pristine, maintenance is key. Start by washing it gently. Use cold water and a mild detergent to avoid fading.
Air drying is the best option. Lay it flat on a clean surface or hang it up to dry naturally. This helps preserve the fabric’s texture and prevents shrinkage.
Ironing can be tricky, so check the fabric type first. If it’s delicate, opt for a low heat setting or steam instead of direct contact with an iron.
Store your hijabhoojup in a cool, dry place away from sunlight to prevent discoloration. A breathable garment bag works wonders for protection against dust.
Handle it with care when wearing and taking off. Avoid snagging on accessories or rough surfaces to maintain its beautiful appearance longer.
Conclusion
Mastering the art of hijabhoojup not only allows for personal expression but also opens the door to creativity and style. The DIY approach empowers you to choose fabrics, colors, and patterns that resonate with your personality. Whether you’re dressing up for a special occasion or looking for an everyday look, this guide provides all the steps needed to create your unique hijabhoojup.
Remember that practice makes perfect. Don’t hesitate to experiment with different styles and embellishments as you become more comfortable in creating your designs. As you hone your skills, you’ll find joy in crafting looks that reflect who you are while embracing cultural significance.
With proper care and maintenance, your hijabhoojup can become a staple piece in your wardrobe, showcasing both functionality and flair. So grab those materials and get started on this exciting journey into the world of DIY hijabhoojup!
TOPIC
What Pet Psychics Can Reveal About Your Animal Companion

Pets are more than just animals—they’re family. They comfort us in difficult times, share in our joys, and often seem to sense our moods better than some humans. But what if there was a way to truly understand what your pet is thinking or feeling? That’s where pet psychics come in.
Pet psychics use their intuitive abilities to connect with animals on an energetic level, helping to bridge the communication gap between humans and their animal companions. Whether you’re concerned about behavioral issues, seeking comfort after a loss, or simply curious about your pet’s thoughts, a session with a pet psychic can offer profound insight and emotional clarity.
Understanding Their Emotions
Like humans, pets experience a wide range of emotions. They can feel joy, anxiety, grief, confusion, and even frustration—but unlike humans, they don’t have the language to express these feelings. Pet psychics tap into an animal’s energy field to interpret their emotional state and understand what might be triggering certain behaviors.
For example, if your dog suddenly becomes withdrawn or your cat starts acting aggressively, it may not be a simple training issue. It could be a response to a change in their environment, a physical discomfort, or even a reflection of emotional energy they’re picking up from their human family members. A pet psychic can help uncover these root causes, allowing you to better care for your animal friend both physically and emotionally.
Pet readings are also especially valuable for adopted or rescued animals whose histories are unknown. By connecting with your pet’s energy, a psychic may reveal past experiences that help explain present-day behavior—and offer guidance on how to help your companion feel safe and loved.
Messages From Your Pet
One of the most heartwarming aspects of working with a pet psychic is receiving direct messages from your animal. These messages may come through as emotions, images, sensations, or even specific phrases interpreted by the psychic. Whether it’s a living pet or one who has passed on, hearing a message of love, reassurance, or gratitude can bring deep emotional healing and a renewed bond.
Many people turn to psychic phone readings for immediate access to gifted psychics who specialize in animal communication. These sessions can be incredibly moving—shedding light on your pet’s needs, their role in your life, and the unspoken ways they support you.
And because every pet and situation is different, California Psychics offers a wide range of psychic readings online, allowing you to find a reader who aligns with your intentions—whether that’s understanding behavior, connecting with a lost pet, or receiving a message from a beloved companion on the other side.
Final Thoughts
Animals have a lot to say—they just need the right translator. Pet psychics offer a unique opportunity to connect with your animal companion on a deeper, more intuitive level. Through energy reading and emotional insight, you can better understand their needs, support their well-being, and strengthen the lifelong bond you share. Whether through psychic phone readings or personalized psychic readings online, your pet’s voice is waiting to be heard.
TOPIC
Why You Should Work with a Vendor-Neutral ERP Advisor for Your Digital Transformation
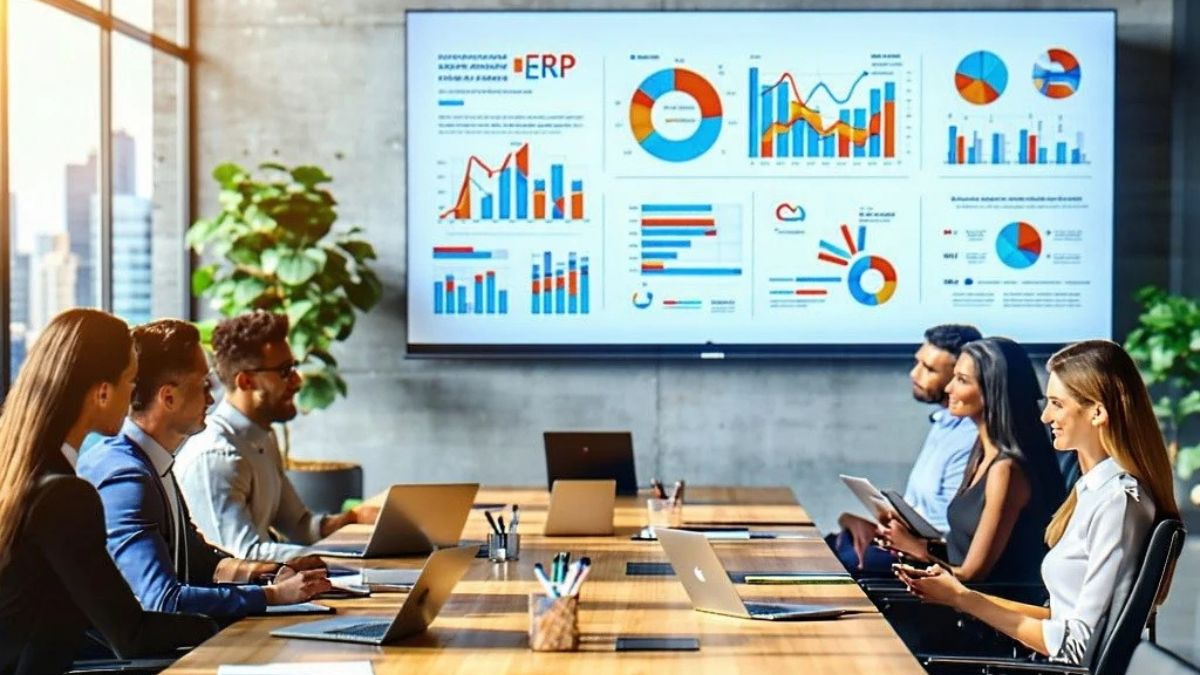
In today’s competitive and rapidly evolving business landscape, selecting the right enterprise resource planning (ERP) system isn’t just a matter of comparing software features—it’s a strategic move that can determine your company’s agility, efficiency, and scalability for years to come. That’s why more organizations are turning to vendor-neutral ERP advisors to guide them through the ERP journey with transparency and objectivity.
Unlike traditional consulting firms that often have hidden alliances with software vendors, vendor-neutral ERP advisors prioritize one thing: your business goals. Their independence allows them to offer unbiased recommendations, negotiate better deals, and ensure you implement an ERP system that truly fits your needs.
If you’re planning an ERP selection or implementation, here’s why it’s in your best interest to work with a vendor-neutral ERP advisor to safeguard your investment and accelerate long-term success.
What Does It Mean to Be Vendor-Neutral?
A vendor-neutral ERP advisor operates with complete independence from ERP software providers. They don’t accept referral commissions, implementation kickbacks, or reseller incentives. This means they are not motivated by profit-sharing arrangements with software vendors—but instead by your company’s outcomes.
Where many traditional consultants subtly guide clients toward preferred vendors, a vendor-agnostic advisor bases their recommendations strictly on what works best for your workflows, industry requirements, IT infrastructure, and strategic roadmap.
1. Eliminate Bias and Protect Your Investment
Choosing an ERP system is a high-stakes decision, often involving six- or seven-figure budgets and long-term commitments. The last thing your organization needs is advice tainted by a consultant’s financial ties to a software vendor.
An unbiased advisor:
- Objectively compares all viable ERP options
- Focuses on aligning the solution to your operational needs
- Avoids over-customization, vendor lock-in, and unnecessary features
By working with an independent partner, you minimize the risk of ending up with a solution that’s either too rigid or over-engineered.
2. Get the Best-Fit Solution—Not the Most Marketed One
Not all ERP platforms are created equal, and what’s popular isn’t always what’s best for your business. A vendor-neutral ERP consultant will help you narrow down systems based on deep, data-driven analysis rather than flashy demos or sales pitches.
They:
- Conduct comprehensive business process reviews
- Identify functional gaps and overlapping tech stacks
- Lead structured RFP (Request for Proposal) processes
- Evaluate vendor responses without bias
- Facilitate scorecard-driven vendor comparisons
This methodology ensures the selected ERP aligns with your budget, growth goals, and industry-specific workflows.
3. Negotiate from a Position of Strength
Vendor-neutral consultants are seasoned negotiators. Because they’re not trying to preserve a cozy relationship with any software company, they can:
- Push for license discounts and implementation savings
- Spot hidden fees or vague SLAs
- Negotiate favorable payment terms and future-proof contracts
Some clients report saving hundreds of thousands of dollars simply because their advisor wasn’t afraid to go toe-to-toe with vendors in pricing and legal negotiations.
4. Strategic Implementation Oversight
The job of a great ERP advisor doesn’t end at selection. Vendor-neutral firms often stay on as implementation partners, overseeing:
- Change management planning
- Project governance
- System integration
- Data migration
- Training programs
They act as your internal advocate, ensuring the implementation team sticks to timelines, doesn’t cut corners, and delivers business value—not just a functional system.
5. Redesign Processes Before Automating Them
A common mistake in ERP deployments is automating inefficient processes. Independent advisors often begin with business process improvement (BPI)—optimizing workflows, removing redundancies, and redefining roles before any software is deployed.
This approach:
- Reduces the need for expensive customizations
- Makes user adoption smoother
- Ensures the ERP enhances—not replicates—your legacy inefficiencies
6. Avoid Post-Go-Live Pitfalls
ERP failure isn’t always about bad software—it’s about misalignment, poor communication, or rushed deployment. Independent consultants help you plan for post-launch success by:
- Establishing metrics for value realization
- Ensuring data quality
- Conducting post-implementation audits
- Driving continuous process improvements
This long-term partnership mindset ensures you keep evolving with the ERP, instead of stagnating post-deployment.
7. Ideal for M&A, Scaling, or Legacy Replacement
Vendor-neutral ERP consultants shine in high-stakes scenarios like:
- Mergers & acquisitions (needing tech consolidation)
- Global expansion (with localized compliance needs)
- Legacy system sunset (migrating from outdated software)
- Recovery from past ERP failures
They’re equipped to handle complexity, multi-vendor ecosystems, and cross-functional teams—all while maintaining focus on your enterprise strategy.
What to Look for in a Vendor-Neutral ERP Advisor
When evaluating potential advisors, prioritize those who:
- Are financially unaffiliated with ERP vendors
- Have multi-platform expertise (SAP, Oracle, NetSuite, Microsoft, Infor, etc.)
- Provide references and case studies across industries
- Offer both selection and implementation support
- Follow proven, repeatable methodologies
- Emphasize business outcomes, not just system deployment
Final Thoughts: Make the Smarter Choice
Your ERP project will shape your company’s operational backbone for the next decade. Choosing a vendor-affiliated consultant might seem convenient, but it can cost you dearly in the long run. Working with a vendor-neutral ERP advisor gives you the strategic, unbiased, and client-first support you need to ensure a successful transformation.
Before you sign a contract or schedule a demo, make sure you’re partnering with someone who sits on your side of the table—not the vendor’s.
Looking for a trusted, independent consultant to help you make the right ERP decision? Work with a vendor-neutral ERP advisor to gain the clarity, confidence, and competitive edge your organization deserves.
About the Author
Vince Louie Daniot is a digital strategist and ERP content specialist. With a background in SaaS marketing and a deep passion for enterprise technology, Vince helps organizations navigate the complex world of ERP selection, implementation, and optimization. His writing blends SEO precision with real-world business insight to educate decision-makers and empower digital transformation. When he’s not crafting long-form content, you’ll find him exploring emerging tech trends or consulting on B2B growth strategies.
TOPIC
Why Investing In A Quality Outdoor Dining Set Is Worth It
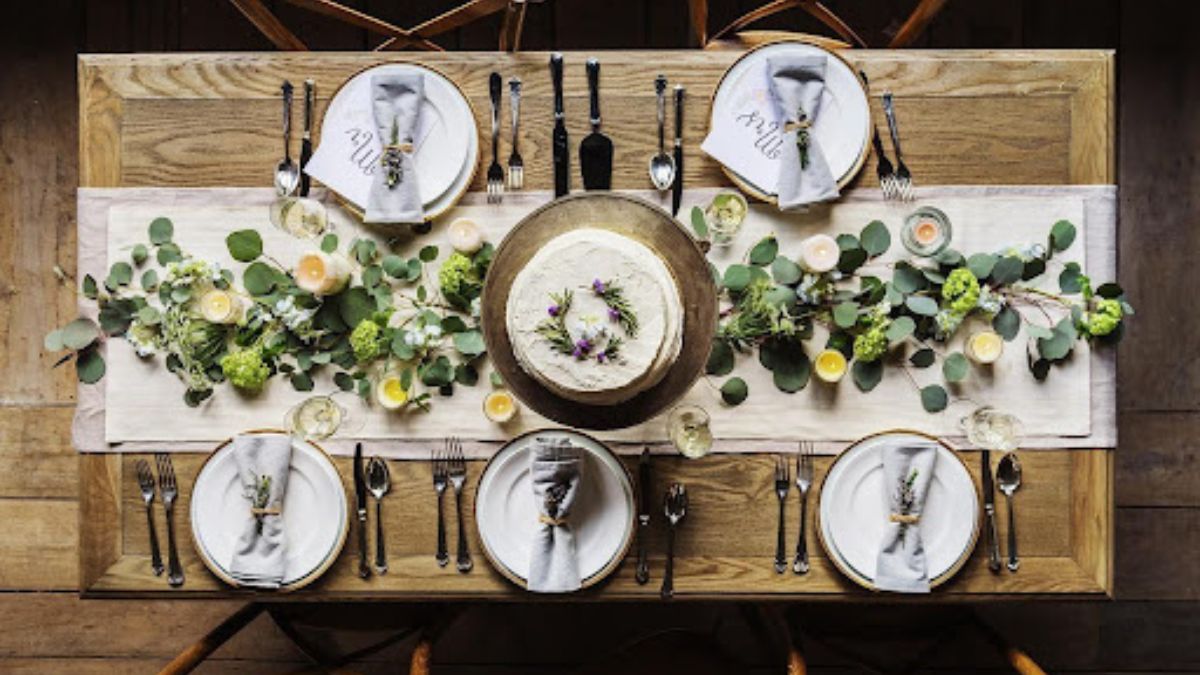
Eating outside is best when the sun is shining, and the breeze is cool. It’s a great way to interact with others and have fun, whether it’s a family BBQ, a quiet brunch, or a wild night with friends. But you need the proper setup to really enjoy these times. That’s why investing in a good outdoor dining set is worth it.
Many individuals don’t see the importance of outdoor furniture because they assume it’s simply an extra. But buying a sturdy and stylish dining set can change the look of your outdoor space. It makes things feel more special, welcoming, and comfy.
Let’s talk about why it’s worth acquiring an excellent outdoor dining set.
1. Boosts Your Outdoor Living Experience
An ideal outdoor dining set will make your balcony or garden feel like an actual room. It’s no longer just a place to hang laundry or grow plants. Instead, it becomes a part of your home where you can relax, dine, laugh, and make memories.
Picture yourself sitting in a comfortable chair with the morning sun on your face and drinking coffee or sitting around a strong dining table and telling stories while eating grilled chicken. A well-made set gives you the chance to live outdoors more often.
You’ll spend more time outside because the furniture is comfortable and suited to the weather. Every time you go into your yard, it feels like a tiny vacation. It’s hard to beat that level of peace and happiness.
2. Lasts Longer and Saves You Money Over Time
It’s tempting to buy an inexpensive plastic table and chairs at the store down the street. They’re not too expensive and they look fine. But they won’t last. They break, fade, or fall apart after one or two rainy seasons. After that, you would have to pay more to get new ones.
However, a good outdoor dining set is made from robust materials like teak wood, powder-coated aluminum, or wicker that can be used in all weathers. These materials can withstand mildew, rain, and even the sun. If you take care of it, a good set can endure for 5, 10, or even 15 years.
In the long run, you save money even though you pay more up front. You also don’t have to worry about the burden of having to buy new chairs or tables every year because they break or wobble.
3. Increases Your Home’s Value and Appeal
Want to know a secret? People love to buy homes with outdoor spaces. Real estate experts claim consumers are more likely to purchase homes with lovely patios or decks. What makes those outside spaces so special? A fashionable dining set.
Making your home comfortable and functional adds actual value to it, even if you don’t plan to sell it soon. It shows that you care, have good taste, and pay attention to little things. Your yard will seem so inviting that guests will be impressed.
A good outdoor dining set draws people in. People naturally come together around it, giving the area a sense of life. Making your yard feel like a real living space is a good idea, whether you’re renting, selling, or just enjoying it.
4. Perfect for Hosting and Entertaining
A good dining set is a must-have if you like having company around. It gives you a space to eat, play games, or sit and talk. If you don’t have enough seats, your guests might have to stand or sit on uncomfortable benches or folding chairs, which is not fun.
With a strong table and comfortable chairs, you can create the perfect place for birthday celebrations, Sunday brunch, or romantic dinners. If you add cushions, fairy lights, or even an umbrella, your outdoor space will be ready for a party in no time.
When everyone gets a great seat at a lovely table, even modest parties feel more special. You don’t have to make a reservation at an expensive restaurant.
5. Improves Mental Health and Wellbeing
Imagine this: You’re outside, the sun is shining on your skin, birds are singing, and you have a hot cup of tea in your hands. It’s quiet, you feel better, and it helps you heal.
Being outside has been shown to lower stress and improve mood. If you have a pleasant location to sit and rest, you’re more likely to experience those benefits frequently. A good outdoor eating set makes this possible.
You could eat breakfast outside or read a book in the sun instead of browsing through your phone all day on the couch. This would promote good behaviors like being aware of your surroundings, getting fresh air, and having actual discussions.
6. Requires Less Maintenance Than You Think
Many individuals think that outdoor furniture is hard to clean. The good news is that high-quality outdoor dining sets are made to be easy to care for. That means you won’t have to spend hours every weekend cleaning or fixing them.
Materials like treated wood, powder-coated aluminum, or synthetic wicker are engineered to withstand rain, wind, and sun. To keep things looking new, wipe them down with a moist cloth. Some sets even have cushions you can take off and wash.
If you take care of your dining set occasionally, it will last for years. This means you can spend more time outside and less time cleaning.
Conclusion
A good outdoor dining set is more than simply furniture; it’s a way to make your house more comfortable and happier. It makes your environment more enjoyable, saves you money over time, and brings people together in meaningful ways. The perfect arrangement makes all the difference, whether you’re throwing a party, spending quiet mornings alone, or just appreciating nature.
If you’ve been wondering whether it’s worth it, the answer is yes. If you take care of your outdoor space, you will be glad you did when you went outside.
-
TOPIC8 months ago
7 Expert Tips For Choosing The Best Basement Renovation Companies
-
BUSINESS2 months ago
Top 5 Features of Sowix Online That Every User Should Know About
-
TOPIC3 weeks ago
Why Greece Katz Martian Has Everyone Talking in 2025
-
TOPIC2 months ago
Top Features of BetterThisWorld .com You Need to Know About
-
FINANCE5 months ago
How TraceLoans Can Simplify Your Finances
-
BIOGRAPHY5 months ago
From Reality Star to Business Mogul: Prince Narula Digital PayPal
-
EDUCATION2 months ago
The Evolution of Pi123: How It Became a Must-Have Tool
-
TOPIC2 months ago
Sabsastaa.com: Your Ultimate Guide to Budget Shopping and Savings